更多關(guān)于粉末壓片模具的相關(guān)信息,請(qǐng)點(diǎn)擊圖片查看
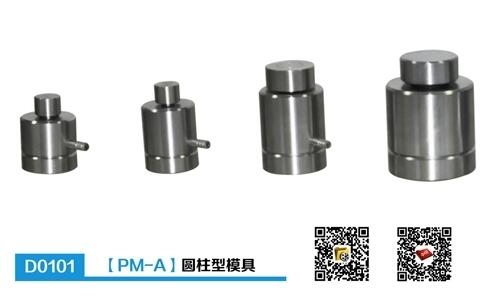

精拓儀器,將堅(jiān)持以“精益求精、開拓創(chuàng)新”的理念,以可靠的儀器質(zhì)量、完善的售后服務(wù)、產(chǎn)品持續(xù)優(yōu)化為客戶提供可靠的、全面的、長期的解決方案!接下來精拓儀器的小編為您分享下粉末壓片模具常見問題及解決方法,希望能幫助你更好的使用粉末壓片模具。

1、藥片重量不穩(wěn)定,片重差異大
原因與解決辦法:藥片的重量不穩(wěn)定,如果定期檢查導(dǎo)軌沒有大的磨損的話,一般zui重要的原因是物料的顆粒不均勻,均勻性不好,藥片的片重差異一定是比較大的。一個(gè)zui簡單的方法,用同體積的30目的細(xì)粉與原粉做比較,如果質(zhì)量相差比較大,一般片差會(huì)比較大。所以解決片重差異的問題,一般都是解決顆粒的問題比較多。
1.1、沖模不規(guī)則的跳動(dòng)比較大。 a、沖模太松(沖??妆仨毥?jīng)過仔細(xì)清理,沖模在沖孔當(dāng)中能自由移動(dòng),但不能出現(xiàn)沖模在自由狀態(tài)下下落的情況)。
b、過大的壓力導(dǎo)致設(shè)備振動(dòng)。c、控制重量的導(dǎo)軌磨損或者松動(dòng)。d、下沖鎖緊裝置調(diào)整不正確。e、防塵圈失效。f、生產(chǎn)速度過高。g、沖模片重定量導(dǎo)軌沒有定量作用,或者被磨損,或者沒有正確安裝。
1.2、中模正常充填后,物料丟失或者再次充填。 a、沖模安裝異常,造成藥粉流失。b、壓料板或刮料板異常。c、過大的真空吸塵。
1.3、加料器缺粉或者堵塞。a、進(jìn)料通道安裝異常。b、物料在料斗中“架橋”。c、充填導(dǎo)軌安裝錯(cuò)誤。d、多次再循環(huán)使用的藥粉。
1.4、在中模充滿之前下沖被拉下來 a、多次再循環(huán)使用的藥粉。b、定量導(dǎo)軌磨損或者變形。
1.5、刮粉器刮粉效果不好 a、刮粉器刮片彎曲,磨損或者不平,彈簧的彈力不好。
1.6、沖模的長度不一致。
1.7、沖模高于沖盤:需要檢查沖盤孔的底部是不是沒有清理干凈,或者中模的高度超差。
1.8、自動(dòng)片重控制系統(tǒng)沒有起作用,認(rèn)真查看說明書,看操作是否有問題。
1.9、沖模的尾部(含斜面部分)差別太大,填充深度不一致。認(rèn)真檢查沖模斜面部分的尺寸,確定沖模尾部的尺寸一致。藥片的厚度不一致
2.0、有可能重量不一致造成,見第1條原因。
2.1、壓輪的跳動(dòng)比較大:首先可能是藥片的密度過大,需要增加厚度或者減少充填量;壓輪不轉(zhuǎn)動(dòng),沖頭的工作條件很差;由于壓輪的負(fù)載過大而造成磨損。
2.2、沖頭的長度不一致。
2、藥片的密度不一致,脆碎度也不一致
2.1 、有可能上面兩個(gè)原因造成。
2.2、藥粉中料斗當(dāng)中分層,物料下落不暢;藥粉多次回收使用,造成一些物料的流動(dòng)性不好;料斗當(dāng)中顆粒和粉末分層,需要減少顆粒的大小差異,降低設(shè)備的振動(dòng),降低設(shè)備生產(chǎn)速度。
2.3、水分含量太低,需要增加水分含量也可以增加附料。
3、壓片機(jī)振動(dòng)太大
3.1、傳動(dòng)皮帶磨損。
3.2、沖頭的長度不一致,或者沖?;煅b。
3.3、壓片操作壓力使藥片的密度接近zui大值,即藥片接近不可壓縮。
3.4、壓片推出時(shí)力量太大。 a、出片導(dǎo)軌磨損b、物料當(dāng)中需要增加附料,也可以在中模內(nèi)孔倒角,降低出片時(shí)的壓力。c、中??讖疆?dāng)中被壓出環(huán)型,出片阻力較大。
3.5、壓力設(shè)置不正確,壓力設(shè)置達(dá)到了沖模承載壓力的極限值。
4、藥片有黑點(diǎn)
4.1、物料當(dāng)中有灰塵、污垢或者是潤滑油。
4.2、需要經(jīng)常清理壓片機(jī),保護(hù)設(shè)備干凈。
4.3、潤滑油設(shè)置量太,或者潤滑油使用不正確。由經(jīng)驗(yàn)來講,使用不正確的潤滑油導(dǎo)致黑點(diǎn)多的原因經(jīng)常出現(xiàn)。一般潤滑油需要有抗腐蝕性,抗氧化性,分水性,抗泡性,更需要有優(yōu)良的極壓及抗磨損性能。如果油的質(zhì)量不好,設(shè)備在使用或者停用一段時(shí)間后,油的潤滑性能降低,首先可能導(dǎo)致設(shè)備磨損,另外油和藥粉產(chǎn)生的污垢也可能增加,然后由于離心力甩出來,造成藥片的黑點(diǎn)多。
4.4、沖頭的防塵圈不正確,或者鍵槽沒有堵塞。
4.5、加料器當(dāng)中由于部件的研磨出現(xiàn)黑物。
4.6、沖頭和中模之間有粘合物,掉落到?jīng)_盤上面,導(dǎo)致黑點(diǎn)。
4.7、物料的特性可能造成黑點(diǎn)。由于物料和沖盤或者刮粉器的摩擦造成有黑斑產(chǎn)生。這種現(xiàn)象產(chǎn)生的黑斑與物料當(dāng)中的黑點(diǎn)不同,它產(chǎn)生的黑斑面積比較大,黑的程序也沒有黑點(diǎn)明顯。這種情況下,需要調(diào)大加料器與沖盤的間隙,并且將刮料板的彈簧彈力減小,降低物料的摩擦力,減少黑點(diǎn)。必要的情況下,需要調(diào)整加料器同沖盤的間隙為入口低出口高,降低物料在加料器當(dāng)中的摩擦力,同時(shí)將刮料板與沖盤調(diào)整為間隙式的,避免摩擦,將加料器襯底和與沖盤接觸部件改為非金屬材料,zui大程度的避免摩擦。
4.8、粉塵比較大的原因?qū)е律蠜_桿上部的防塵圈下有粉塵與潤滑油的結(jié)塊。即使用zui大的吸塵機(jī)也很難解決小黑點(diǎn)的問題。這個(gè)時(shí)候一般要求上沖加食用的潤滑脂,如食品級(jí)的高溫鏈條油,潤滑脂一般不易流動(dòng),潤滑上沖帽的時(shí)間比較長。在安裝沖頭的時(shí)候就在沖帽上加上潤滑脂。另外必須是大壓力大風(fēng)量的吸塵機(jī),將沖盤旋轉(zhuǎn)起來后的揚(yáng)塵全部吸走。這些都可以減少黑點(diǎn)的產(chǎn)生。要*的避免黑點(diǎn),應(yīng)當(dāng)在出片后的位置在中盤的上表面增加一套吸塵裝置,保證從上沖盤或者其它位置來的臟物全部吸走,而且不能影響藥粉的回流,也不能吸走加料器當(dāng)中的藥粉,這樣可以保證沒有黑點(diǎn)。
5、設(shè)備漏粉過多
5.1、沖盤和加料器底盤的間隙調(diào)整不正確。加料器底盤安裝太高而不平;也有可能是加料器底盤由于先前磨損而造成間隙,導(dǎo)致漏粉。
5.2、刮料板安裝不正確,導(dǎo)致粉漏;有可能刮料板彎曲;與螺紋連接導(dǎo)致單邊較高;壓緊彈簧壓力不夠,壓料板抬高導(dǎo)致刮料板與沖盤有間隙。
5.3、刮料板刮粉不足,起不到應(yīng)有的效果;刮料板可能磨損;也有可能是彈簧的彈力不足。
5.4、從上沖入中模之前漏粉,上沖頭部高于中模,而沒有及時(shí)進(jìn)入中模。
5.5、在沖壓藥片處漏粉。a、沖模精度低,間隙大,導(dǎo)致漏粉。b、由于壓片的成型位置太高,出現(xiàn)漏粉。c、在壓片的位置真空吸力太大,或者是吸管位置安裝不正確。
5.6、藥粉過細(xì),導(dǎo)致漏粉。a、中模的孔徑和下沖頭的外徑間隙太大;b、藥粉太細(xì),或者藥粉當(dāng)中的細(xì)顆粒太多。c、中模的倒角安裝位置不對(duì),導(dǎo)致物料從斜面處漏粉。這種情況和加料器、平臺(tái)、壓料板和中沖盤的間隙有關(guān)。卸下加料器,用刀口尺檢查平臺(tái)和中沖盤的間隙,應(yīng)當(dāng)不超過0.08mm。檢查壓料板與中沖盤面的縫隙,貼緊無間隙。檢查中沖模是否有高出中沖盤的情況,應(yīng)調(diào)平或低0.02mm以內(nèi)。用千分尺檢查中沖盤的端面跳動(dòng)是否過大,應(yīng)不超過0.08mm。
粉末壓片模具的使用注意事項(xiàng):
為了保證模具的正常使用,請(qǐng)用戶嚴(yán)格按照壓片模具使用說明操作:
1、每一次使用后,須將模具部件上及壓頭上粘掛的粉末消除掉,如果清洗的不干凈,可能造成使用中壓頭卡死。
2、一般被測物品都有一定的腐蝕性,不及時(shí)的清除干凈,可能造成模具表面生銹,易造成壓頭裝偏,損壞模具。
3、如長期不使用,須將模具清洗干凈,涂防護(hù)油放入干燥器中。
4、壓頭是用硬質(zhì)合金材料加工研磨制成的,有著很高的強(qiáng)性,和一定的易碎性,出廠前經(jīng)過嚴(yán)格的測繪及打壓試驗(yàn),只要用戶嚴(yán)格按照使用說明書規(guī)定的壓力范圍內(nèi)使用不會(huì)造成壓頭的損壞。
5、通常使用模具,一般zui高打壓到12噸,即可滿足用戶要求。